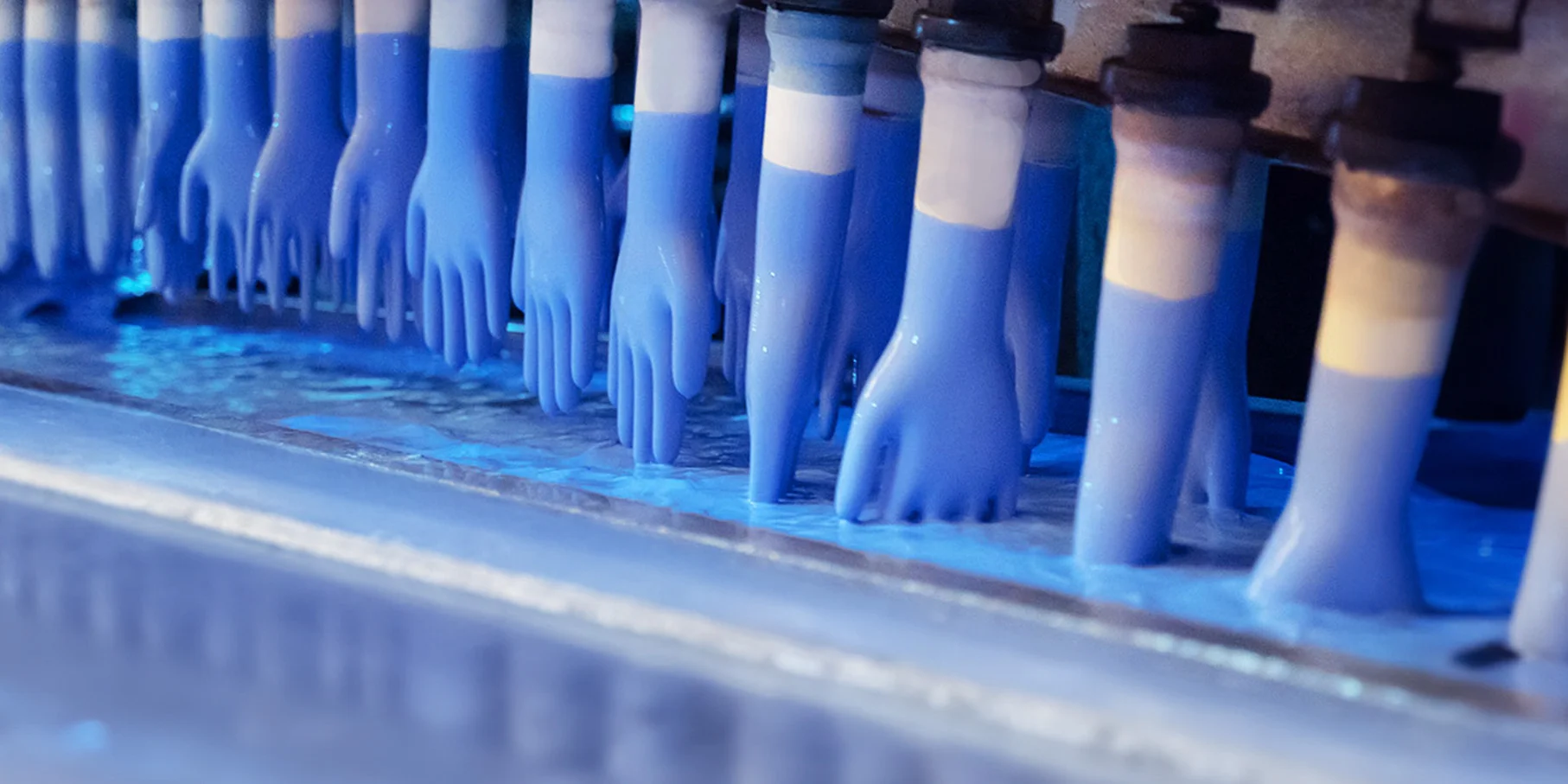
Chemical accelerators play a crucial role in glove production, enhancing the efficiency and quality of the manufacturing process. These compounds are essential to the vulcanization of rubber, which gives gloves their durability and elasticity. The use of accelerators also significantly impacts the speed and effectiveness of glove manufacturing, making it possible to meet the growing global demand for protective handwear.
Understanding the types and functions of chemical accelerators is vital for both manufacturers and consumers. This article explores the various accelerators used in glove production, their role in vulcanization, and potential health concerns such as Type IV hypersensitivity reactions. It also delves into alternatives to traditional accelerators, like carboxylic acid derivatives, which are being developed to address safety issues. By examining these aspects, readers will gain insight into the complexities of glove manufacturing and the ongoing efforts to improve product safety and performance.
Types of Chemical Accelerators Used in Glove Manufacturing
Chemical accelerators play a crucial role in the vulcanization process of rubber gloves. The most commonly used chemical accelerators in glove manufacturing fall into three main categories: thiurams, dithiocarbamates, and mercaptobenzothiazoles.
Thiurams
Thiurams are a class of chemical accelerators that have been widely used in the rubber industry. Examples of thiurams include Tetramethylthiuram Disulphide (TMTD), Tetramethyl Thiuram Disulphide (TMTM), and Tetraethyl Thiuram Disulfide (TETD) [1]. However, thiurams have been associated with a high incidence of allergic reactions. In fact, they are responsible for about 80% of Type IV allergies related to rubber products [2]. Due to this health concern, some manufacturers have taken steps to eliminate thiurams from their production processes. At Eastwest Medico, we completely refrain from using thiuram accelerators in our products.
Dithiocarbamates
Dithiocarbamates are another important class of chemical accelerators used in glove production. Common examples include Zinc Dibutyldithiocarbamate (ZDBC), Zinc Dimethyldihiocarbamates (ZDMC), Zinc Diethyldithiocarbamates (ZDEC), Zinc pentamethylene Dithiocarbamate (ZPMC), and Zinc Pentamethylene Dithicarbamate (ZPD) [1]. These compounds are not only used as accelerators in the manufacture of natural latex rubber products but are also found in various fungicides [3].
Studies have shown that handling salad produce with gloves containing natural latex rubber products can result in the deposition of reportable levels of dithiocarbamates. This contamination risk is highest when ‘worn’ gloves are used [3]. To avoid any possibility of contamination, it is recommended that gloves containing any rubber should not be used for handling produce at any stage during the harvesting, grading, or distribution phases of production [3].
Mercaptobenzothiazoles
Mercaptobenzothiazoles (MBT) form the third major category of chemical accelerators used in glove manufacturing. This group includes compounds such as Zinc Mercaptobenzothiazole (ZMBT), Mercaptobenzothiazole (MBT), and Benzothiazyl Disulphide (MBTS) [1]. MBT is primarily used in the rubber industry as a non-volatile vulcanization accelerator and as an intermediate in producing other accelerators [4].
Research has shown that MBT can cause allergic contact dermatitis from gloves and other rubber products [5]. When exposed to occupational oxidants such as hypochlorous acid, iodine, and hydrogen peroxide, MBT undergoes oxidative transformation to form MBTS within the glove matrix [5]. This transformation and subsequent reactions with proteins may contribute to the allergenic properties of MBT.
In an older study of various rubber products from 2005, ZMBT was found in 9 out of 19 gloves tested, with amounts ranging from 0.15 to 1.5 µmol/g of glove material [4]. Today, 20 years later, most glove manufacturers have moved away from using Mercaptobenzothiazoles, as presence of these accelerators in gloves can lead to potential health concerns for users, particularly those with sensitive skin or prone to allergies.
It’s important to note that the use of chemical accelerators in glove manufacturing is a complex issue that involves balancing production efficiency with potential health risks. As awareness of these risks grows, manufacturers are increasingly exploring alternatives to traditional chemical accelerators to produce safer, hypoallergenic gloves while maintaining the necessary quality and durability of their products.
Role of Accelerators in the Vulcanization Process
Chemical accelerators play a crucial role in the vulcanization process of rubber gloves, transforming raw rubber into a more durable and resilient material. These compounds are added to the rubber latex/NBR mixture to enhance the efficiency and quality of glove production [1]. The use of accelerators in glove manufacturing has a significant impact on the final product’s performance and characteristics.
Speeding up crosslinking reactions
The primary function of chemical accelerators is to speed up the vulcanization process. These compounds significantly reduce the time required for glove production by accelerating the crosslinking reactions between rubber molecules.
Different types of accelerators are used in the industry, each with its specific properties and effects on the vulcanization process. Some of the most commonly used accelerators include:
- Thiurams: Are used in glove production to improve the curing process and enhance the elasticity and strength of the gloves.
- Mercaptobenzothiazole: Contributes to improving the tensile strength and elasticity of gloves.
- Dithiocarbamates: Are frequently employed to enhance the curing process and increase gloves’ chemical resistance.
Improving physical properties
Accelerators significantly enhance the physical properties of rubber gloves. They make the gloves firmer, more elastic, and more resistant to various hazards. This improvement in physical properties is crucial for ensuring the durability and functionality of the gloves in various applications.
The use of accelerators results in gloves with:
- Increased tensile strength
- Enhanced elasticity
- Improved tear resistance
- Better overall durability
These improved physical properties are essential for producing high-quality gloves that can withstand the rigors of daily use in various industries, from healthcare to manufacturing.
Enhancing chemical resistance
Another important aspect of accelerators in glove production is their ability to enhance the chemical resistance of the final product. This property is particularly crucial for gloves used in industries where exposure to harsh chemicals is common.
Dithiocarbamates, for example, are known to increase the chemical resistance of gloves [6]. This enhanced resistance helps protect the wearer’s hands from potentially harmful substances, making the gloves more effective in various industrial and laboratory settings.
It’s important to note that while accelerators offer numerous benefits in glove production, they also have potential drawbacks. There is a growing concern about occupational health risks associated with the frequent use of gloves containing chemical accelerators [1]. Compounds such as carbamates, thiurams, 2-mercaptobenzothiazole (MBT), and 1,3-diphenylguanidine (DPG) in rubber gloves have been identified as contributing factors to contact allergies [1].
Table 1: Common Chemical Accelerator Compounds Used in Rubber Glove Vulcanization
Accelerator Type |
Examples |
Primary Functions |
---|---|---|
Thiurams |
TMTD, TMTM, TETD |
Improve curing, enhance elasticity and strength |
Mercaptobenzothiazoles |
MBT, ZMBT |
Improve tensile strength and elasticity |
Dithiocarbamates |
ZDBC, ZDMC, ZDEC |
Enhance curing process, increase chemical resistance |
As the industry continues to evolve, manufacturers are exploring alternative methods and compounds to achieve the benefits of accelerators while minimizing potential health risks. This ongoing research aims to strike a balance between production efficiency, glove performance, and user safety.
Health Concerns Associated with Chemical Accelerators
The use of chemical accelerators in glove production has raised significant health concerns, particularly among healthcare workers and other frequent glove users. These concerns primarily revolve around allergic reactions and skin sensitivities caused by exposure to these chemicals.
Type IV Delayed Hypersensitivity
Type IV delayed hypersensitivity reactions are a common health issue associated with chemical accelerators in gloves. These reactions are cell-mediated and typically occur 6 to 48 hours after exposure to the allergen [7]. Unlike immediate allergic reactions, delayed hypersensitivity may not be noticeable during the first exposure but can develop over time with repeated contact [7].
The symptoms of Type IV reactions often manifest as contact dermatitis, characterized by redness, swelling, small blisters, and itching [7]. In chronic cases, individuals may experience dry skin, thickening of the skin, peeling, and open lesions [7]. It’s important to note that these symptoms can worsen in the days following initial contact with the allergen.
Allergic Contact Dermatitis
Allergic contact dermatitis is a significant concern related to chemical accelerators in gloves. This condition occurs when the skin comes into contact with allergens present in glove components [7]. Studies have shown that medical gloves are one of the most frequent causes of occupational allergic contact dermatitis, especially among healthcare workers [8].
Vulcanization accelerators are the most common culprits in allergic contact dermatitis cases related to gloves. In fact, approximately 80% of allergic contact dermatitis cases associated with single-use gloves are linked to these accelerators [7].
A study of 23 patients with allergic contact dermatitis due to rubber accelerators in gloves found that each patient had positive patch test reactions to one or more accelerators, including carbamates, thiurams, 2-mercaptobenzothiazole, and 1,3-diphenylguanidine [8]. This highlights the variety of chemicals that can trigger allergic reactions in sensitive individuals.
Can Accelerators be Effectively Removed from Gloves?
In response to the growing concern over allergic contact dermatitis, many glove manufacturers have introduced accelerator-free products [9]. However, it’s important to note that tests have shown that gloves branded as “accelerator-free” might still contain accelerators[9]. This is because some companies market their accelerator-free based on test reports showing that accelerators are non-detectable by water and acetone extraction. However, these gloves may still cause allergic reactions in people with Type IV allergies. A glove should only be accepted as Accelerator-Free if the manufacturer can show a declaration that no accelerators have been used in the compounding.
Accelerators still play a vital role in the vulcanization process, which gives gloves their desired properties, such as barrier performance, tensile strength, and elasticity [9]. Without these chemical accelerators, many of the qualities sought in natural rubber latex and most synthetic gloves would not be present.
While accelerator-free gloves may help reduce the prevalence of allergic contact dermatitis, caution is advised when offering these gloves to individuals with known sensitivities to specific chemical accelerators [9]. The effectiveness of accelerator removal can vary, and more research is needed to compare the allergenic content of accelerator-free gloves with standard medical gloves, particularly those claiming low residual accelerators and low dermatitis potential [9].
To address these health concerns, it’s recommended that individuals suspected of having a Type IV allergy immediately change glove types and wear gloves known to be low in residual chemicals and chemical contact sensitizers [7]. Additionally, wearing cotton or nylon inner-gloves can help reduce the risk of allergic reactions [7].
Alternatives to Traditional Chemical Accelerators
Accelerator-free formulations
The glove manufacturing industry has been exploring alternative solutions in response to growing health concerns associated with chemical accelerators. A new generation of nitrile gloves has emerged, offering products free from traditional chemical accelerators. These accelerator-free gloves have been developed to address the issue of Type IV allergies caused by chemical accelerators commonly used in non-latex glove production. We have written a thorough article about accelerator-free gloves on this LINK.
Future directions
The chemical accelerators market for rubber gloves is expected to grow significantly between 2023 and 2031 [12]. This growth is driven by increasing demand across various applications, including natural rubber latex gloves and nitrile gloves [12]. However, the industry is also shifting towards more sustainable and safer alternatives.
Research and development efforts are focusing on:
- Improving formulation accuracy to ensure final products perform as expected [13].
- Enhancing process automation from the R&D stage through production [13].
- Developing solutions that reduce manual operator intervention and increase final product quality [13].
To achieve these goals, manufacturers are investing in advanced equipment and technologies. For instance, process analytical technology (PAT), such as inline particle analyzers, in-situ spectroscopy, and reaction calorimeters, can provide critical insights into how processes will perform at scale [13]. These tools help create “process fingerprints” that inform inline monitoring and troubleshooting, ultimately leading to maximum yield and consistent quality [13].
As the industry continues to evolve, we are likely to see further innovations in accelerator-free formulations. These advancements will aim to strike a balance between production efficiency, glove performance, and user safety, addressing the growing demand for safer and more environmentally friendly glove options.
Conclusion
Chemical accelerators significantly impact glove production, enhancing efficiency and quality while also raising health concerns. These compounds speed up vulcanization, improve physical properties, and boost chemical resistance, but they can also trigger allergic reactions in some users. This balance between benefits and risks has led manufacturers to explore new options, aiming to create safer gloves without sacrificing performance.
As the industry progresses, there’s a growing focus on developing accelerator-free formulations. These advancements are set to shake things up in glove manufacturing, potentially offering safer alternatives for those with sensitivities. Moreover, ongoing research and tech improvements are paving the way to boost production efficiency and product quality while addressing safety concerns. In the end, these efforts are likely to result in gloves that are safer and more effective for a wide range of uses.
FAQs
What types of accelerators are commonly used in glove manufacturing?
The primary accelerators utilized in producing single-use gloves include Thiurams, Dithiocarbamates, and Benzothiazoles.
What does it mean when gloves are labeled as ‘accelerator-free’?
Accelerator-free nitrile gloves are produced without chemical accelerants. They are crafted from the same basic materials as standard nitrile gloves but with an altered formula that excludes accelerators, making them more suitable for users and environmentally friendly.
What are the common causes of glove allergies?
Latex proteins and accelerators found in natural rubber products often cause glove allergies. These allergies can usually arise from direct skin contact, highlighting the importance of using hypoallergenic gloves for those with sensitive skin.
Are all nitrile gloves accelerator-free?
Not all nitrile gloves are free of accelerators. Traditional nitrile gloves may still contain residual accelerators like thiurams and carbamates, which can lead to contact dermatitis in some users. Accelerator-free gloves, however, do not have these chemicals and are thus a safer choice for individuals with sensitive skin or latex allergies.
References
[1] – https://munglobal.com.au/knowledge-hub/chemical-accelerators-in-rubber-gloves/[2] – https://www.sempermed.com/knowledge-area/allergies/[3] – https://projectbluearchive.blob.core.windows.net/media/Default/Horticulture/Publications/Dithiocarbamate%20contamination%20of%20salad%20produce%20and%20the%20use%20of%20rubber%20gloves.pdf[4] – https://ec.europa.eu/health/ph_risk/committees/04_sccp/docs/sccp_o_00i.pdf[5] – https://pubs.acs.org/doi/abs/10.1021/tx700139g[7] – https://www.shieldscientific.com/glove-education/allergic-contact-dermatitis-type-iv-and-its-implications-for-single-use-gloves/[8] – https://jamanetwork.com/journals/jamadermatology/fullarticle/421910[9] – https://www.shieldscientific.com/wp-content/uploads/distibutor_resources/News-Letters/English/4%20Accelerator%20Free%20gloves%20EN%20neutral%20Version%204.pdf[12] – https://www.linkedin.com/pulse/chemical-accelerators-rubber-gloves-market-analysis-tbnaf[13] – https://www.mt.com/us/en/home/applications/Top_application_browse/glove-production.html