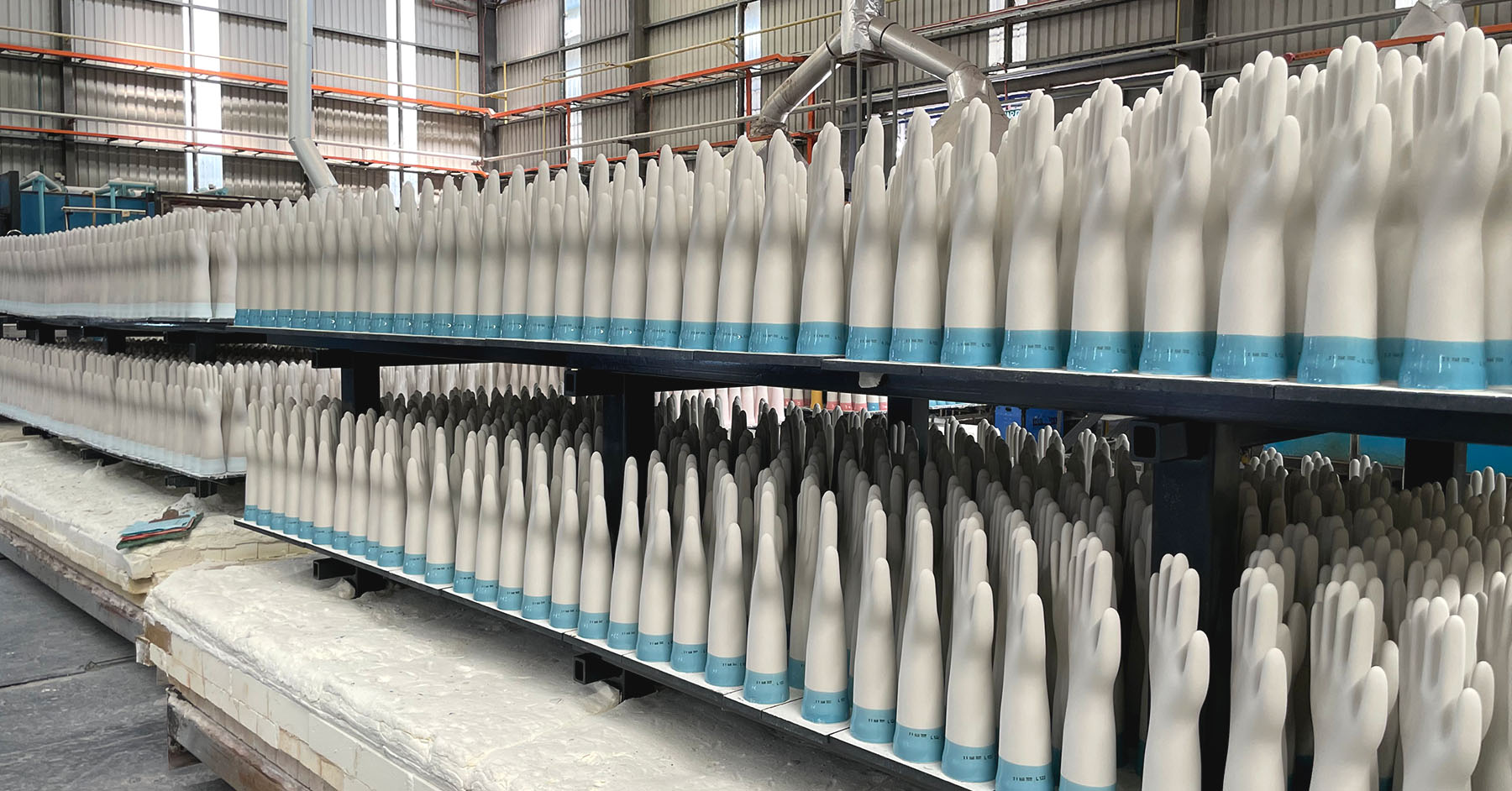
Nitrile gloves are multi-purpose chemical-resistant gloves made from synthetic rubber and oils. Nitrile is a type of rubber known for its many use cases. But how do you make nitrile gloves? Let’s take a look at how nitrile gloves are manufactured. We all know that manufacturing processes in any company can get complicated. But it doesn’t have to be so scary or difficult to understand. For example, the process isn’t as complicated as you might think when it comes to manufacturing nitrile gloves. That being said, some components are still involved in making any product, no matter how simple or complex it seems. Keep reading to understand this process better and see what goes into making nitrile gloves.
Understanding the Manufacturing Process of Nitrile Gloves
Every manufacturing process has a few key steps. These steps can differ depending on the type of product being manufactured, but the general framework is always the same:
- We have the materials or inputs phase. This phase refers to the raw materials that go into making the product.
- Then there is the processing phase, where the materials are transformed into a usable product. The processing phase refers to the machines or tools used to make the product.
- Finally, there is the outputs phase, where the product is packaged and sold.
The inputs phase is often referred to as the supply chain, which is the process of getting the materials or raw materials to the factory. The processing phase is also known as the transformation phase because it transforms the materials into a product. The outputs phase is also sometimes referred to as the distribution phase because it refers to distributing the product after it is made.
Mixing the Raw Materials
The first step of the processing phase is mixing the raw materials. The manufacturers will mix a list of ingredients to create the synthetic rubber used to make the gloves. The main ingredient in nitrile gloves is NBR (Nitrile Butadiene Rubber), but the gloves also contain other chemicals such as sulfur, antifoaming agents, stabilizers, and accelerators. As the name describes, accelerators are used to accelerate the process of making nitrile gloves. Recently some manufacturers have started producing gloves without accelerators to minimize the risk of Type IV hypersensitivity, which accelerators in rare cases have shown to provoke. If you already know that you have Type IV hypersensitivity or simply want the best of the best, look for “Accelerator-Free” or ask your vendor if the gloves are made without accelerators. Click the link to learn more about Accelerator-Free Nitrile Gloves.
Shaping the Gloves
After mixing the ingredients, the next step is shaping the gloves. The manufacturers will transform the ingredients into gloves by using a machine that shapes the gloves. This shaping process can be done in several different ways, depending on the design of the machine. Most production lines have rotating steel rollers with ceramic glove formers mounted.
Starting with a wash, the ceramic hand-shaped formers are dipped in water and bleach to ensure that they are clean and that no residues from the previous production-run are present. After the formers are dried, they are dipped in calcium carbonate and calcium nitrate solution to help the synthetic rubber to coagulate. The formers are now dipped in the synthetic rubber mixture (NBR-mix), which coats the formers with what will turn out to be the final glove.
Drying and Solidifying the Gloves
Next, the gloves must be dried and solidified. The gloves are dried in a machine that removes all the water. The gloves are then put into an oven set at a low temperature to solidify them. Any product made with synthetic rubber has to be dried and solidified before it can be used. This is because synthetic rubber is technically plastic, not rubber. This means that it is not yet fully transformed into rubber. It is still semi-liquid, which is why it is called synthetic rubber. To fully transform the synthetic rubber into rubber, the gloves must be dried and solidified in an oven.
Coating and Stripping the Gloves
When Nitrile gloves are produced, two additional processes may be used to improve donning (donning = putting on the glove). These processes are called polymer coating and chlorination. Polymer coating adds a lubricating layer to the glove’s surface, while chlorination makes the material slicker and harder by exposing the glove to a chlorine-acid mixture.
Next is the stripping phase, where the gloves are removed from the formers.
Quality Assurance
Quality assurance is where the gloves are checked for physical and visual defects like pinholes and black or white spots from the production. This kind of test is often referred to as the AQL test. The manufacturers will also verify the thickness of the gloves, chemical composition, and elasticity, which will also be checked for accuracy and consistency. On a scheduled basis, the gloves will be tested to see if they are resistant to chemicals and other elements.
Very often a third party company is used for tests. We always use SGS or TüV to make AQL inspections for every batch of PROSENSO gloves.
When all tests are passed, the gloves can be packed in boxes or polybags and sent to the distributors.
Summing up
The manufacturing process of nitrile gloves is quite simple. Once you know what each step entails, it’s not hard to understand. Once you understand all the different components that go into making a product, you’ll be able to see how everything fits together. Nitrile gloves are a staple within many industries, and they’re used for a wide range of tasks. Nitrile gloves are used by workers in a variety of industries, such as healthcare, automotive, and manufacturing.