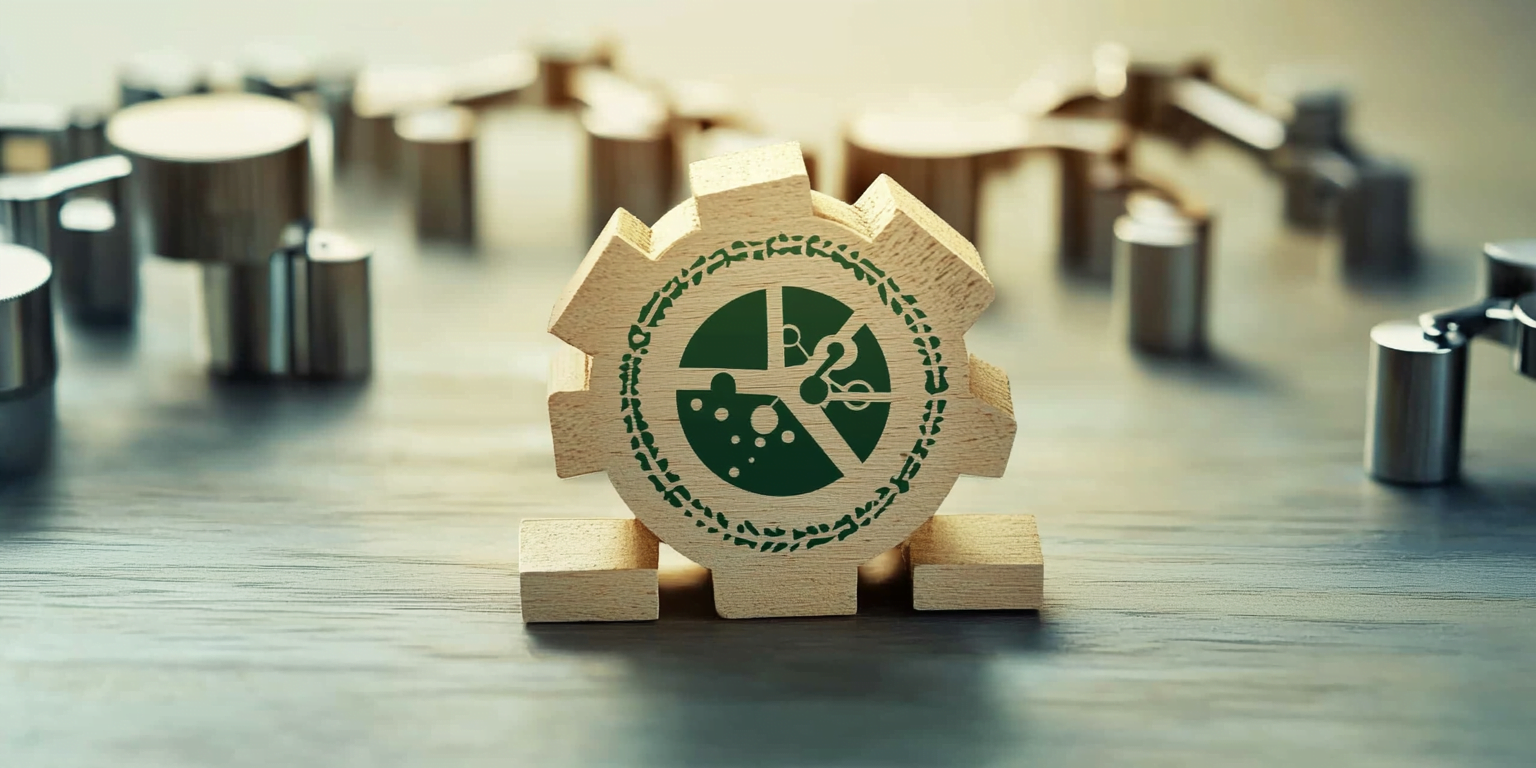
In today’s environmentally conscious world, understanding the environmental impact of products has become crucial. Life cycle assessment (LCA) studies, guided by ISO 14040 standards, play a vital role in evaluating the carbon footprint of various industries, including glove manufacturing. These studies provide valuable insights into the environmental effects of gloves throughout their lifecycle, from raw material extraction to disposal, helping manufacturers and consumers make informed decisions.
LCA studies in glove manufacturing encompass different approaches, such as Cradle to Gate, Gate to Gate, and Cradle to Grave analyzes. Each method offers unique perspectives on the environmental impact of gloves, with a focus on key stages of production and use. This article delves into the types of LCA studies used in glove manufacturing, explores important environmental impact categories, compares results across different glove materials, and highlights best practices for conducting thorough and accurate assessments in this industry.
Types of Life Cycle Assessment Studies in Glove Manufacturing
Life cycle assessment (LCA) studies in glove manufacturing employ various approaches to evaluate the environmental impact of products throughout their lifecycle. These studies, guided by ISO 14040 standards, provide valuable insights into the carbon footprint and resource efficiency of gloves. Let’s explore the three main types of LCA studies used in the industry.
Cradle-to-Gate LCA
Cradle-to-gate LCA focuses on the environmental impact from raw material extraction to the factory gate, before the product reaches the consumer. This approach has an influence on assessing the initial stages of glove production, including material sourcing and manufacturing processes. For instance, a study on nitrile glove production in Malaysia, China, and France employed a cradle-to-gate assessment to compare the carbon footprint of gloves from different origins [1]. The study took into account greenhouse gas emissions from raw material extraction to glove storage in European warehouses, revealing that sea freight transport to Europe represented 6-8% of the total glove footprint [1].
Gate-to-Gate LCA
Gate-to-gate LCA examines a specific value-added process within the production chain. This method has an impact on analyzing the environmental effects of individual manufacturing stages, such as molding or packaging. By focusing on a single phase, manufacturers can identify areas for improvement in their production processes. For example, some studies have used gate-to-gate analysis to optimize energy consumption and reduce greenhouse gas emissions in glove manufacturing [2].
Cradle-to-Grave LCA
Cradle-to-grave LCA provides a comprehensive evaluation of a product’s environmental impact throughout its entire lifecycle, from resource extraction to disposal. This approach has an influence on understanding the long-term effects of glove production, use, and disposal. A study comparing reusable and disposable protective garment sets, including gloves, utilized a cradle-to-grave approach to assess their environmental performance [3]. The analysis included manufacturing, laundering, end-of-life treatment, and associated transport between phases [3].
Each LCA approach offers unique insights into the environmental impact of glove manufacturing. Cradle-to-gate studies help manufacturers optimize production processes, while gate-to-gate analyzes focus on specific stages for targeted improvements. Cradle-to-grave assessments provide a holistic view of a product’s lifecycle, enabling informed decision-making regarding sustainability.
By employing these various LCA methodologies, glove manufacturers can gain a deeper understanding of their products’ environmental footprint and identify opportunities for enhancing sustainability throughout the supply chain. This knowledge has an impact on driving innovation in materials, production techniques, and disposal methods, ultimately leading to more environmentally friendly glove manufacturing practices.
Key Environmental Impact Categories in Glove LCAs
Life cycle assessment (LCA) studies in glove manufacturing focus on several key environmental impact categories to evaluate the sustainability of different products and processes. These categories help manufacturers and consumers understand the comprehensive environmental footprint of gloves throughout their lifecycle.
Global Warming Potential
Global warming potential (GWP) is a crucial metric in glove LCAs, measuring the contribution of greenhouse gas emissions to climate change. The manufacturing process has been identified as the largest contributor to CO2 emissions in glove production [1]. A cradle-to-gate assessment of nitrile glove production in Malaysia, China, and France revealed that gloves made in France had a 25% lower carbon footprint compared to those produced in Malaysia and China [1] at the time of the study in 2022. This difference way attributed to variations in energy sources and production efficiency. The active use of these studies has helped improve Asian manufactures, which now can provide results similar to those of the western manufacturers.
Water Consumption
Water footprint is another significant environmental impact category in glove LCAs. The water consumption for different glove materials varies greatly. For instance, cotton gloves have a substantially higher water footprint compared to nitrile or latex gloves. A study found that cotton gloves consume over 400 liters of water throughout their lifecycle, while nitrile and latex gloves use less than 0.5 liters each [4]. This vast difference is primarily due to the intensive irrigation required for cotton cultivation, particularly in water-scarce regions like India.
Energy Use
Energy consumption is a critical factor in assessing the environmental impact of glove manufacturing. LCA studies have shown that utilities, particularly commercial electricity for heating purposes, contribute significantly to the overall environmental impact and cost of glove production [2]. For example, a simulated base case scenario for nitrile butadiene rubber (NBR) glove manufacturing required 5847.1274 kW of power for heating leaching water in a single unit operation [2]. Optimizing energy use and exploring alternative energy sources can significantly reduce the environmental footprint of glove production.
Waste Generation
The generation and management of waste is an important consideration in glove LCAs, especially given the increased use of personal protective equipment (PPE) during the COVID-19 pandemic. Improper disposal of biomedical waste and healthcare waste can lead to environmental contamination and pose risks to human health [5]. The extensive use of predominantly non-degradable plastics in PPE has led to their accumulation in landfills, with potential consequences for marine environments through the formation of microplastics [5].
To address these environmental impacts, manufacturers and users are exploring various strategies. Some companies have implemented zero waste-to-landfill targets and waste management programs aimed at minimizing waste creation and maximizing reuse and recycling [6]. Additionally, the development of alternative materials and more sustainable production processes is ongoing to reduce the overall environmental footprint of glove manufacturing.
By considering these key environmental impact categories in LCA studies, glove manufacturers can make informed decisions to improve their products’ sustainability and contribute to a more environmentally friendly industry.
Comparing LCA Results Across Different Glove Materials
Life cycle assessment (LCA) studies provide valuable insights into the environmental impact of various glove materials. By comparing the results across different types of gloves, manufacturers and users can make informed decisions about which materials are most sustainable. Let’s examine the LCA results for natural rubber, nitrile, and vinyl gloves.
Natural Rubber Gloves
Natural rubber gloves, also known as latex gloves, are derived from rubber plantations primarily located in Southeast Asia. These gloves offer excellent comfort, tensile strength, and elasticity. From an environmental perspective, natural rubber gloves have some advantages. They are biodegradable and have a relatively low carbon footprint during production. However, the manufacturing process can be energy-intensive, which has an impact on their overall environmental performance.
A cradle-to-gate assessment comparing latex gloves made in Thailand and Malaysia with nitrile gloves produced in France revealed that latex gloves had a comparable carbon footprint to nitrile gloves manufactured in the same region [1]. However, it’s important to note that the energy mix used in production can significantly affect the glove’s carbon footprint.
Nitrile Gloves
Nitrile gloves, made from a synthetic rubber copolymer, have gained popularity due to their chemical resistance and durability. LCA studies have shown that nitrile gloves can have a lower environmental impact compared to natural rubber gloves, depending on the manufacturing location and energy sources used.
A study found that nitrile gloves produced in France had a 25% lower carbon footprint than those made in Malaysia or China [1]. This difference can be attributed to variations in energy sources and production efficiency. The two main sources of CO2 emissions in nitrile glove production are:
- The production of nitrile resin, where the weight of the glove and the country of resin production are key factors.
- The energy used in glove manufacturing, with low-carbon electricity and carbon-free steam being crucial for reducing the footprint.
When comparing the environmental impact of different glove materials, it’s crucial to consider factors beyond just production. For instance, the end-of-life stage of gloves can significantly contribute to their overall environmental footprint. Incineration, a common disposal method for hospital gloves, can add approximately 12 gCO2eq per glove to its carbon footprint [1].
To reduce the environmental impact of glove use, hospitals and other institutions can consider strategies such as local purchasing, choosing gloves with lower unit weights, and exploring alternative end-of-life options that respect safety concerns related to potential pathogen contamination [1].
Best Practices for Conducting Glove Manufacturing LCAs
Conducting a comprehensive life cycle assessment (LCA) for glove manufacturing requires careful planning and execution. By following best practices, manufacturers can ensure accurate and meaningful results that drive sustainable improvements in their production processes.
Data Collection Methods
Accurate data collection is crucial for a reliable LCA. Manufacturers should gather detailed information on raw materials, energy consumption, and production processes. This includes quantifying inputs such as acrylonitrile butadiene rubber for nitrile gloves or natural rubber for latex gloves. Energy usage during manufacturing, particularly for heating and drying processes, should be meticulously recorded. For instance, a simulated base case scenario for nitrile butadiene rubber glove manufacturing required 5847.1274 kW of power for heating leaching water in a single unit operation [2].
To ensure data quality, manufacturers should:
- Utilize automated data collection systems where possible
- Implement rigorous quality control measures
- Collaborate with suppliers to obtain accurate upstream data
- Conduct regular audits to verify data accuracy
Choosing Appropriate System Boundaries
Defining clear system boundaries is essential for a comprehensive LCA. The scope can vary from cradle-to-gate, focusing on raw material extraction to factory output, to cradle-to-grave, which includes the entire lifecycle up to disposal. For glove manufacturing, it’s crucial to consider all relevant stages, including:
- Raw material extraction and processing
- Manufacturing processes
- Packaging and distribution
- Use phase (if applicable)
- End-of-life management
When determining system boundaries, manufacturers should consider the geographic location of production facilities and suppliers. For example, a study comparing latex gloves made in Thailand and Malaysia with nitrile gloves produced in France revealed significant differences in carbon footprint due to variations in energy sources and production efficiency [1].
Interpreting and Reporting Results
Once data has been collected and analyzed, proper interpretation is key to deriving actionable insights. Manufacturers should:
- Conduct sensitivity analyses to identify key factors influencing environmental impact
- Perform contribution analyses to determine which processes or materials have the most significant environmental effects
- Compare results across different glove materials and production methods
Transparency is crucial when reporting results. Manufacturers should communicate the scope, assumptions, and limitations of their LCA. For instance, a cradle-to-gate assessment of nitrile glove production in Malaysia, China, and France revealed that gloves made in France had a 25% lower carbon footprint compared to those produced in Malaysia and China [1]. However, recently announced LCA studies from the top-tier manufacturers in both Malaysia and Thailand have shown that carbon emissions can be greatly improved and fully on par with Western manufacturers.
By adhering to these best practices, glove manufacturers can conduct robust LCAs that provide valuable insights into their environmental impact. This information can then be used to drive sustainable improvements in production processes, material selection, and waste management strategies, ultimately leading to more environmentally friendly glove manufacturing practices.
Conclusion
Life cycle assessment studies have become a crucial tool for glove manufacturers to evaluate and improve their environmental impact. These studies offer valuable insights into the carbon footprint and resource efficiency of different glove materials and production methods. It’s worth noting that manufacturers use various LCA approaches, such as Gate to Gate, Cradle to Grave, and Cradle to Gate, depending on their specific goals. While the manufacturing process remains the largest contributor to CO2 emissions across all study types, understanding the differences between these approaches is key to making accurate comparisons.
Moving forward, the glove industry faces both challenges and opportunities in its journey toward sustainability. By leveraging LCA findings, manufacturers can pinpoint areas for improvement, from raw material selection to end-of-life management. This knowledge impacts driving innovation in production techniques, energy efficiency, and waste reduction strategies. As environmental concerns continue to shape consumer preferences and regulatory landscapes, the insights gained from LCA studies will play a vital role in shaping the future of glove manufacturing.
FAQs
What does LCA stand for in the context of manufacturing?
Life Cycle Assessment (LCA) is a detailed method used to evaluate the environmental impacts associated with all the stages of a product’s life, from raw material extraction through materials processing, manufacture, distribution, use, repair and maintenance, and disposal or recycling. It helps in understanding the comprehensive environmental consequences of industrial activities.
References
[1] – https://cdn.prod.website-files.com/6151b650ce4cd9198b1fd7e8/64d01341d93ac10636f7dc91_Life_Cycle_Analysis_Nitrile_gloves_ECOVAMED_May-2022.pdf[2] – https://www.researchgate.net/publication/333220153_Life_Cycle_Optimization_for_Synthetic_Glove_Manufacturing[3] – https://www.unitechus.com/wp-content/uploads/2019/09/UniTech-LCA-Report-final-10-18-2013.pdf[4] – https://stich.culturalheritage.org/nitrile-latex-cotton-gloves/[5] – https://www.ncbi.nlm.nih.gov/pmc/articles/PMC10421242/[6] – https://cleanroomtechnology.com/understanding-sustainability-and-the-role-glove-manufactures-should[7] – https://www.ncbi.nlm.nih.gov/pmc/articles/PMC8041744/